Unlocking Operational Excellence in Small & Medium Enterprises
For the ambitious small and medium-sized enterprise (SME), embracing modern methodologies to streamline operations is not just a strategic move – it’s essential for survival. One methodology that has been making waves in the world of big corporations is Lean Six Sigma. But the pertinent question for SMEs is: Can this large-scale methodology be tailored for smaller businesses? Let’s dive deep.
What is Lean Six Sigma?
To fully appreciate its potential for SMEs, we must first understand Lean Six Sigma. Originating from Japanese manufacturing and popularized by giants like General Electric, this methodology is essentially a marriage between Lean and Six Sigma, two separate ideals and practices. Lean Six Sigma is a method that relies on a collaborative team effort to improve performance by systematically removing waste and reducing variation. It combines the principles of two powerful methodologies:
Lean: Originated from the Toyota Production System and focuses on reducing waste (activities that don’t add value). The core idea is to maximize customer value while minimizing waste. It aims to create more value for customers with fewer resources. Simply put, Lean is a strategy focusing on eliminating waste in all processes.
Six Sigma: Developed by Motorola in 1986, it’s a disciplined, data-driven approach and methodology for eliminating defects in any process – from manufacturing to transactional and from product to service. The central idea behind Six Sigma is to measure defects and get as close to “zero defects” as possible. The term “Six Sigma” refers to the statistical representation of only 3.4 defects out of one million opportunities. Six Sigma is simple, a discipline that emphasizes reducing variability in processes to enhance product quality.
Together, Lean Six Sigma seeks to optimize processes, reduce variability, and eliminate waste or non-value-added steps. This combined approach ensures efficiency and quality, making it a favorite amongst various industries seeking operational excellence. When combined, Lean Six Sigma provides a robust framework for businesses to drastically improve efficiency, eradicate wasteful practices, and maintain consistent product or service quality.
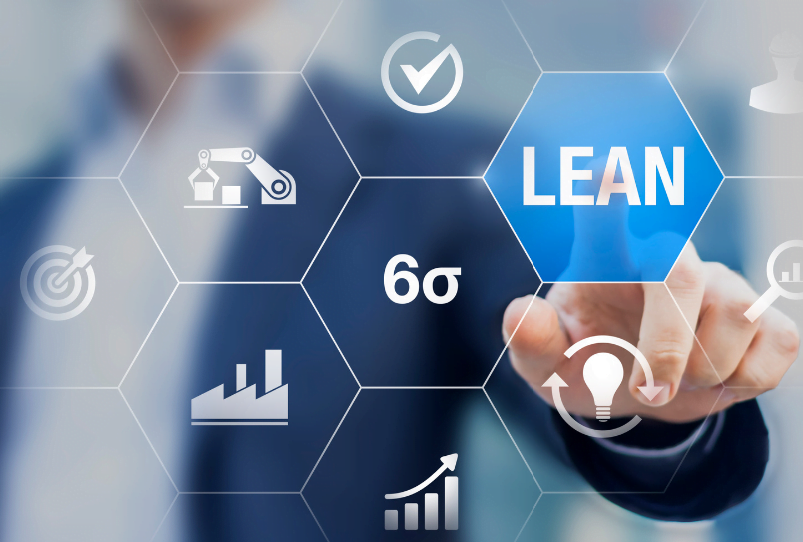
Hesitations Among SMEs
Many SMEs are wary of Lean Six Sigma, often due to:
- The seeming complexity of its tools and methodologies.
- A fear of high initial implementation costs.
- An assumption that it requires a large, specialized team to manage.
However, these hesitations often arise from misinterpretations or half-understood facts about how adaptable Lean Six Sigma truly is.
Lean Six Sigma and SMEs: A Match Made in Efficiency Heaven
Here’s why this approach is a goldmine for small and medium enterprises:
- Quick Flexibility and Adaptability: One significant advantage SMEs have over large corporations is agility. SMEs can swiftly adapt to new methodologies and practices, meaning the benefits of Lean Six Sigma can be realized sooner.
- Cost Efficiency & Waste Reduction: For SMEs, even small inefficiencies can have outsized effects on the bottom line. Lean’s focus on waste reduction can translate into substantial savings. Even minimal waste can significantly impact an SME’s bottom line. Lean Six Sigma’s emphasis on waste reduction can translate to substantial cost savings.
- Enhanced Customer Satisfaction: With Six Sigma’s quality-centric approach and by refining processes and improving quality, SMEs can deliver better products and services, enhancing customer loyalty and satisfaction and brand reputation.
Implementing Lean Six Sigma in SMEs
Here are a few considerations when implementing Lean Six Sigma
- Leadership Commitment: Any major initiative must have the backing of top management. Leaders need to understand, commit to, and champion Lean Six Sigma principles.
- Employee Training: Rather than hiring a large team, focus on upskilling existing employees. Start with key personnel who can then become in-house champions of the methodology.
- Selecting the Right Projects: Begin with smaller projects that promise tangible benefits. Such “quick wins” not only provide immediate value but also help in building momentum and securing buy-in from the broader organization.
- Data-Driven Decisions: Lean Six Sigma thrives on data. Ensure that you’re collecting relevant data and using it to inform your decisions, highlighting inefficiencies and areas for improvement.
- Regular Reviews: Establish a system for regular reviews. It allows for real-time adjustments, taking advantage of the SME’s innate flexibility.
Celebrate and Institutionalize Wins: Recognizing achievements is vital for morale. But beyond that, successful implementations should be studied and institutionalized, serving as a template for future projects.
Finding Hidden Inefficiencies: The Power of Lean Six Sigma for SMEs
In the dynamic landscape of Small and Medium-sized Enterprises (SMEs), latent inefficiencies—often masked as longstanding procedures or minor bottlenecks—can significantly impede productivity and growth. Often, inefficiencies in business processes remain hidden, accepted as the cost of doing business. This is especially true for SMEs where processes have often evolved organically.
Lean Six Sigma’s rigorous, data-driven approach shines a light on these areas. It offers not just a diagnosis but also prescribes solutions based on best practices. These inefficiencies, while seemingly trivial, accumulate over time, subtly sapping profitability. Lean Six Sigma, with its data-driven approach, empowers businesses to pinpoint and address these inefficiencies.
By using tools like process mapping and voice of the customer (VOC) analysis, SMEs can not only illuminate and eradicate current wasteful practices but also instill a culture of continuous improvement. This proactive stance ensures SMEs remain agile, customer-centric, and primed for sustainable growth.
Challenges to watch out for
While the benefits are numerous, SMEs should also be aware of potential challenges:
- Resistance to Change: As with any new initiative, there might be resistance. Overcoming this requires clear communication about the benefits and ensuring everyone feels they’re part of the journey.
- Overreach: While it’s good to be ambitious, attempting to do too much too soon can be counterproductive. It’s better to have a phased approach.
One additional and significant challenge that must be addressed earlier on is Leadership Alignment. As one of the foundational elements for the successful implementation of Lean Six Sigma, or any significant organizational change initiative, leadership must be aligned and leading the charge. When we refer to leadership alignment, we’re talking about a consistent understanding, commitment, and direction set by leaders at all levels within an organization. All of this must be aligned with business results so garnering support, though crucial should not be a enormously “heavy lift”.
Here’s why leadership alignment is crucial and some considerations:
Unified Vision: For Lean Six Sigma to be truly effective, leaders need to have a unified vision of what they hope to achieve with its implementation. This ensures that everyone is moving in the same direction and towards the same goals.
Resource Allocation: Leaders control resources, both human and financial. Without alignment, necessary resources might not be allocated effectively, hampering the progress of improvement initiatives.
Overcoming Resistance: Change is often met with resistance. Aligned leaders can present a united front, reinforcing the importance and benefits of the new methodologies. Their collective endorsement can help mitigate skepticism or pushback from the teams.
Consistent Communication: When leaders are aligned, the messaging about the Lean Six Sigma initiative remains consistent throughout the organization. This consistent communication prevents confusion and mixed messages, which can derail implementation efforts.
Feedback Loops: Aligned leadership ensures that there’s a structure in place for regular feedback. As the Lean Six Sigma practices are implemented, leaders can collectively assess the progress, discuss challenges, and recalibrate strategies as needed.
Sustainability: For the gains achieved through Lean Six Sigma to be sustainable, there needs to be long-term commitment and consistency in approach. Aligned leadership is pivotal in ensuring that the methodologies and practices are institutionalized and become part of the organization’s fabric.
In essence, without leadership alignment, even the most well-planned Lean Six Sigma initiatives can face unnecessary obstacles, slowing down or even halting the drive towards operational excellence. It’s akin to trying to steer a large ship with multiple captains giving different directions. For smooth sailing, everyone at the helm must be aligned in purpose and action.
Embracing Lean Six Sigma in the SME Landscape – The Road Ahead
In the grand tapestry of business methodologies, Lean Six Sigma stands out for its dual focus on efficiency and quality. While its roots might be in large-scale corporate settings, its principles are universal. The adaptability, focus on data, and emphasis on continuous improvement align perfectly with the needs and strengths of SMEs.
For the forward-thinking SME, the question isn’t whether to implement Lean Six Sigma, but how to do it best. By embracing its principles, SMEs are not just optimizing their operations but also setting the stage for sustainable growth and success.
Remember, methodologies like Lean Six Sigma are tools – their true value is realized in how they are applied. And in the dynamic, ever-evolving world of SMEs, they offer a compass to navigate the complex waters of business operations and management.
Stay connected with “Hey, Lonnie…” for more in-depth insights, strategies, and guidance tailored to the unique world of SMEs. Let’s walk this journey of operational excellence together. Your next leap in business efficiency might be just a blog post away!