In a bustling marketplace in Kyoto, as the sun was beginning to set and shadows elongated, a local vendor named Hiroshi discovered a mysterious scroll buried deep within an old wooden chest. The scroll wasn’t adorned with ancient spells or samurai techniques but with systematic principles—principles that would later resonate with business moguls worldwide. These principles, though not really from an old Japanese marketplace, have a lineage that traces back to innovative companies and are known today as Lean Six Sigma. Here’s how these timeless principles, often associated with large corporations, can be the hidden treasure for small businesses. See the article, Lean Six Sigma Implementation in Small Enterprises, for a deeper dive into Lean Six Sigma.
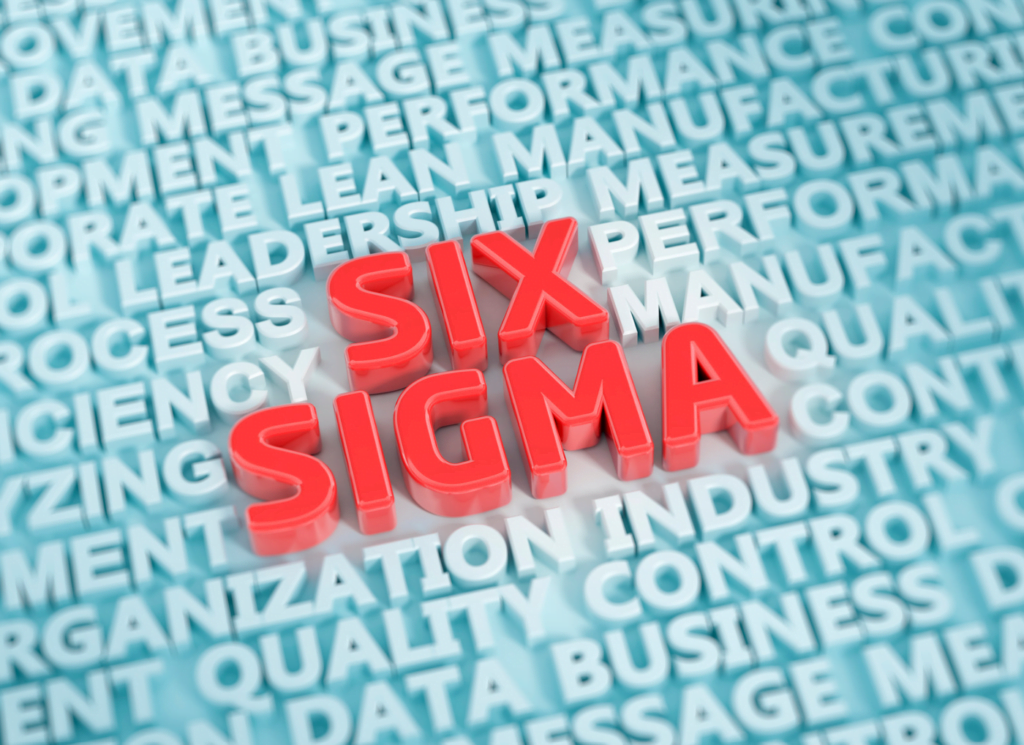
Unraveling the Scroll: What is Lean Six Sigma?
Lean Six Sigma is an amalgamation of two powerful methodologies. The Lean philosophy, stemming from Toyota’s production system, focuses on eliminating waste—any activity not adding value to the end customer. Six Sigma, on the other hand, hailing from Motorola’s vision, zeroes in on reducing process variation, ensuring a high-quality output every time. Combined, they form a potent toolset that ensures efficiency and quality.
Why Small Businesses Need a Piece of This Ancient Wisdom
- Efficiency: Small businesses often run on thin margins. By cutting down waste and streamlining processes, they can do more with less, increasing profitability.
- Consistency: In today’s cutthroat environment, consistency can set a business apart. Six Sigma aims at delivering consistent outputs, ensuring customer trust and loyalty.
- Empowered Employees: Lean Six Sigma doesn’t just impose changes; it involves employees in the change process, leading to empowered, motivated teams.
Decoding the Principles for Small Enterprises
Implementing Lean Six Sigma can feel like deciphering an ancient language. But with the right approach, small businesses can decode and apply these principles effectively.
- Start Small: Instead of a sweeping overhaul, begin by identifying one process that needs improvement. Apply Lean Six Sigma principles there, learn, and then expand to other areas.
- Value Stream Mapping: Draw out your processes visually. This will highlight bottlenecks, delays, and redundancies. Once you see the entire process, it becomes easier to spot areas for improvement.
- Focus on the Customer: Always ask: Does this add value to the customer? If something doesn’t, it might be a candidate for elimination.
Navigating Challenges on the Path
Every treasure hunt has its challenges, and implementing Lean Six Sigma in a small business is no different. Here are some common challenges and how to overcome them:
- Resistance to Change: Change can be unsettling. Involve your team in the process, train them, and highlight the benefits to get their buy-in.
- Limited Resources: Small businesses may not have the resources to hire Six Sigma Black Belts. But many online courses and resources can help bridge this gap.
- Complexity: Some might feel Lean Six Sigma is too complex for a small business. But remember, it’s not about using every tool but about selecting the tools that resonate with your specific needs.
The Treasure at the End
When applied effectively, Lean Six Sigma can be transformative. Processes become smoother, customers are happier, and the bottom line often improves. Moreover, it fosters a culture of continuous improvement, where every employee is on the lookout for better ways of doing things.
As you embark on this journey, remember Hiroshi from our tale. The scroll he discovered wasn’t magical, but the principles it highlighted, when applied diligently, could bring about magic in business operations. Small businesses might not have vast treasures, but in Lean Six Sigma, they have a tool that can unlock immense value.
In wrapping up, the enigmatic beginnings of Lean Six Sigma in our story may be fictional, but its principles’ transformative power is very real. With the insights from “Hey, Lonnie…” and a bit of adventurous spirit, small businesses can harness this power, navigating their way to operational excellence.